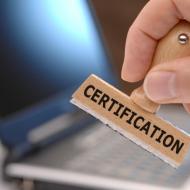
Современные и классические сварочные технологии. Как сделать современные сварочные аппараты своими руками
Одно из важнейших ремесел для человека. С помощью сварочных технологий нам удается создавать по-настоящему удивительные вещи: от простейших бытовых приборов до космических ракет. В этой статье мы расскажем, как происходит сварка, какие существуют виды сварки и их краткая характеристика.
Что такое сварка? Каковы основы сварки? Эти вопросы задаю многие начинающие умельцы. По сути своей, сварка - это процесс соединения разных металлов. Соединение (его также называют ) формируется на межатомном уровне с помощью нагрева или механической деформации.
Теория сварки металлов очень обширна и невозможно в рамках одной статьи описать все нюансы. Также как невозможно описать все способы сварки металлов, поскольку на данный момент способов около сотни. Но мы постараемся кратко классифицировать методы сварки, чтобы новички не запутались.
Итак, на данный момент возможна термическая, термомеханическая и полностью механическая сварка деталей из металла или других материалов (например, или стекла). При выборе способа сварки учитывается каждый нюанс: толщина деталей, их состав, условия работы и прочее. От этого зависит технология сварки металла.
Термическая сварка - это процесс соединения деталей только с помощью высоких температур. Металл плавится, образуется надежное . К термическим методам относится, например, и (о них мы поговорим позже).
Термомеханическая сварка - это процесс соединения деталей с помощью высоких температур и механического воздействия, например, давления. К такому типу принадлежит . Деталь нагревается не так сильно, как в случае обычной термической сварки, а для формирования шва используется механическая нагрузка, а не плавление металла как такового.
Механическая сварка - процесс соединения деталей без применения высоких температур и вообще тепловой энергии. Здесь ключевой элемент - механическое воздействие. К такому типу относится , ультразвуковая сварка или соединение деталей трением.
Также существует классификация способов сварки по техническим признакам. Используя такую классификацию можно довольно кратко описать все имеющиеся типы сварки. Они делятся на:
- Сварку в защитной среде (для защиты может использоваться , инертный газ, активный газ, вакуум, защита может быть комбинированной и состоять из нескольких материалов сразу).
- Сварку прерывистую и непрерывную.
- Сварку ручную, механизированную, полуавтоматическую, автоматическую, роботизированную.
Если вы ранее не сталкивались со сваркой и все перечисленное выше кажется чем-то запутанным и непонятным, то не беспокойтесь. Далее мы расскажем, какие самые популярные методы сварки используются в домашних и промышленных условиях.
Вам будем дана характеристика основных видов сварки и некоторые особенности, которые нужно учесть. Кстати, многим видам сварки мы посвящали отдельные статьи, которые вы можете прочесть, открыв рубрику « » на нашем сайте.
Ручная дуговая сварка с применением неплавящихся электродов
Способ разных металлов с применением неплавящихся электродов - один из самых популярных методов как среди домашних умельцев, так и среди профессионалов своего дела. Ручная дуговая сварка - это вообще один из древнейших способов сварки. Благодаря большому для дуговой сварки такой метод стал доступен широкому кругу сварщиков.
Электрод - это стержень, выполняющий роль проводника тока. Он может быть изготовлен из различных материалов и иметь специальное покрытие.
Технология дуговой сварки крайне проста: детали подгоняют друг к другу, затем электродом постукивают или чиркают о поверхность металла, зажигая сварочную . В качестве основного оборудования используют сварочные инверторы.
Для сварки инвертором выбирают неплавящиеся электроды, сделанные из , вольфрама или . Во время сварки электрод нагревается до высокой температуры, плавя металл и образуя сварочную ванну, в которой как раз и формируется шов. Такой метод используют для сварки цветных металлов.
Ручная дуговая сварка с применением плавящихся электродов
Виды сварки плавлением металла не заканчиваются на применении неплавящихся стержней. Для работы также можно использовать плавящиеся электроды. Технология сварки металла с использованием плавящихся стержней такая же, что и при работе с неплавящимися материалами.
Отличие лишь в составе самого электрода: плавящиеся стержни обычно изготавливаются из легкоплавких металлов. Такие стержни также пригодны для сварки в домашних условиях. Здесь шов образуется не только за счет расплавленного металла детали, но и за счет расплавленного электрода.
Дуговая сварка с использованием защитного газа
Способ дуговой сварки разных металлов с использованием защитного газа выполняется с помощью плавящихся и неплавящихся электродов. Технология сварки такая же, как и при классической ручной дуговой сварке. Но здесь для дополнительной защиты сварочной ванны в зону сварки подается специальный защитный газ, поставляемый в баллонах.
Дело в том, что сварочная ванна легко подвержена негативному влиянию кислорода и под его воздействием шов может окислиться и получиться некачественным. Газ как раз и помогает избежать этих проблем. При его подаче в сварочную зону образуется плотное газовое облако, не дающее кислороду проникнуть в сварочную ванну.
Автоматическая и полуавтоматическая сварка с использованием флюса или газа
Автоматическая и с применением флюса или - это уже более продвинутый способ соединения металлов. Здесь часть работ механизирована, например, подача электрода в сварочную зону. Это значит, что сварщик подает стержень не с помощью рук, а с помощью специального механизма.
Автоматическая сварка подразумевает механизированную подачу и дальнейшее движение электрода, а полуавтоматическая подразумевает только механизированную подачу. Дальнейшее движение электрода сварщик осуществляет вручную.
Здесь защита сварочной ванны от кислорода просто обязательна, поэтому используется газ (по аналогии с дуговой сваркой с применением газов) или специальный . Флюс может быть жидким, пастообразным или кристаллическим. С помощью флюса можно значительно улучшить качество шва.
Прочие методы соединения металлов
Помимо традиционных способов сварки в современной промышленности применяются методы, позволяющие соединить уникальные металлы. Зачастую такие металлы обладают ярко выраженными химическими или тугоплавкими свойствами, отчего привычные способы сварки не подходят для их соединения. Конечно, такие металлы не используются в домашней сварке, но они широко применяются для создания ответственных деталей на крупном производстве.
Мы расскажем про виды сварки плавлением, когда суть сварки заключается в подаче большого количества тепла на маленький участок сварки. К таким методам относится лазерная сварка и плазменная сварка.
металлов выполняется с помощью автоматического и полуавтоматического оборудования. Такой процесс сварки может быть полностью роботизирован и не требует присутствия человека. Здесь деталь нагревается, а затем и плавится под воздействием тепла, исходящего от лазерного луча и направленного в определенную точку.
Тепло концентрируется строго в одной точке, позволяя сваривать очень мелкие детали размером менее одного миллиметра. Также с помощью призмы лазер можно расщепить и направиться в разные стороны, чтобы сварить несколько деталей сразу.
Металлов выполняется с применением ионизированного газа, называемого плазмой. Газ струёй подается в сварочную зону, образовывая плазму. Она работает в связке с вольфрамовым электродом и газ нагревается за счет электрической дуги.
Сам ионизированный газ обладает свойством проводника тока, поэтому в случае плазменной сварки именно плазма является ключевым элементом в рабочем процессе. Также плазма активно защищает сварочную ванну от негативного влияния кислорода. Такой метод сварки используется при работе с металлами, толщиной до 9 миллиметров.
Технологический процесс сварки
Мало знать способы сварки, нужно еще понимать, какие необходимы документы на сварку и из каких этапов состоит сварочный процесс. Конечно, это справедливо только в отношении профессиональных сварщиков, выполняющих работу в цеху или на производстве. Вам это не нужно, если вы собираетесь варить забор на даче, но дополнительные знания тоже не помешают.
Итак, вот наше краткое описание технологического процесса сварки:
- Разработка чертежа
- Составление технологической карты
- Подготовка рабочего места сварщика и подготовка металла
- Непосредственно сварка
- Очистка металла
- Контроль качества
Сам по себе техпроцесс - это полное описание этапов сварки. Технический процесс разрабатывается после того, как будут готовы чертежи будущей металлоконструкции. Чертеж делают, опираясь на (ГОСТы, например), при этом во главу ставят качество будущей конструкции и разумную экономию.
Технологический процесс сварки оформляется на специально разработанных для этого бланках. Стандартный бланк для описания техпроцесса называется «технологическая карта». В технологической карте и описываются все этапы производства. Если производство серийное или крупномасштабное, то изложение может быть довольно подробным, с описанием каждого нюанса.
В технологическую карту заносят тип металла, из которого изготовлены детали, способы сварки металлов, используемые для соединения этих деталей, применяемое для этих целей сварочное или иное оборудование, типы присадочных материалов, электродов, газов или флюсов, используемых в работе. Также указывается последовательность формирования швов, их размеры и прочие характеристики.
Также в технологической карте указывают , их диаметр, скорость их подачи, скорость сварки, количество слоев у шва, рекомендуемые (параметр полярности и величины сварочного тока), указывают марку флюса. Перед самой сваркой детали тщательно подготавливают, очищая их от коррозии, загрязнений и масла. Поверхность металла обезжиривают с помощью растворителя. Если у детали есть значительные видимые дефекты (например, трещины), то она не допускается к сварке.
После сварки предстоит контроль сварочных швов. Этой теме мы посвятили , но здесь кратко расскажем об основных методах контроля. Прежде всего, применяется визуальный контроль, когда сварщик может сам определить наличие дефектов у сварочного соединения. Специалистами проводится дополнительный контроль с помощью специальных приборов (это может быть магнитный контроль, радиационный или ультразвуковой).
Конечно, не все дефекты считаются плохими. Для каждых сварочных работ составляется перечень с дефектами, которые допустимы и не сильно повлияют на качество готового изделия. Контролером может быть сварщик или отдельный специалист. Его имя обязательно указывается в документах, он является ответственным лицом на этапе контроля.
Вместо заключения
В этой статье мы рассказали самое основное. Конечно, мы не сможем перечислить и описать все виды сварочных работ в рамках одной этой статьи, но на нашем сайте вы можете найти материалы, где мы рассказываем все о сварке и объясняем основы сварки различных металлов.
Сварочный процесс формирует неразъемное соединение различных частей каких-либо металлов за счет образования новых межатомных связей.
Он заключается в создании локального или повсеместного прогрева, пластической деформации, или одновременного действия обоих факторов. Современные сварочные технологии представлены почти сотней видов автоматизированной и ручной сварки.
Имеются три разновидности или типа сварки. По методу получения энергии соединения ее делят на термическую, термомеханическую и механическую.
К термической сварке причисляют процессы с использованием электрической дуги, газа, плазмы и других источников теплового излучения. Именно благодаря ему происходит нагрев и сварка.
В термомеханических видах кроме тепловой энергии применяют давление для получения неразрывного соединения.
В механической теплоту получают за счет трения, давления, ультразвука или взрыва.
Виды сварочных работ многообразны и их классификация производится по разным критериям. Классификация идет по способу , по непрерывности процесса сварки, степени механизации, используемым газам. Кроме этого имеются технологические признаки, которые индивидуальны для каждого вида сварки.
Виды сварных соединений подробно описаны в ГОСТ (государственных стандартах). Кроме этого имеется большое количество ГОСТ описывающих виды сваривания, способы контроля сварных швов, меры безопасности при производстве сварочных работ.
Термическое сваривание материалов
Термические процессы основываются на плавлении соединяемых деталей за счет тепловой энергии. Выделяю несколько видов термической сварки:
- электродуговая (в среде защитных газов, под флюсом и прочие);
- электрошлаковая;
- электронно-лучевая и лучевая (лазерная);
- плазменная;
- газовая;
- термитная.
Самое широкое применение получила . Но и другие виды востребованы в различных современных сферах производства и в бытовых условия.
Расплавление электрической дугой
Электродуговой вид сварки работает за счет выделения энергии в дуге из-за того, что сопротивление дуги значительно больше, чем сопротивление всей электрической цепи, образующей замкнутый контур.
Поэтому практически все тепловая энергия выделяется в дуге, разогревая ее до 4,5-6 тысяч градусов и вызывая плавление любого металла. Дуга возникает в зазоре электрода и свариваемого металла, вызывая их плавление.
При остывании создается неразрывный шов, свойства которого связаны с током, составом присадки и многими другими факторами.
Дуговое сваривание производится плавящимися и неплавящимися стержнями (электродами). В оборудовании используется инверторная технология, что позволило создать компактные производительные устройства.
При сварке заготовок с помощью электрода разжигают дугу между ним и поверхностью стыка. Это создается за счет короткого замыкания при прикосновении прутка к металлу, и последующего его отрыва на расстояние 3-5 мм.
Дуга расплавляет конец электрода и кромки свариваемого изделия. В точке образования дуги создается сварочная ванна.
Для получения сварного шва требуется вести электрод вдоль стыка со скоростью достаточной для расплавления кромок и электрода, но не достаточной для прожигания деталей.
После охлаждения металла получается сварной шов по прочности сопоставимый с основой. Электрод может быть в виде отдельного стержня в обмазке или присадочной проволоки на механизме ее подачи.
При сваривании неплавящимся стержнем электродуга возникает между ним и кромками заготовок. Происходит расплавление кромок, если необходимо и присадочной проволоки в образующейся при этом сварочной ванне. Пруток может быть угольным или из вольфрама. Электродом неплавящегося вида обычно работают при (латуни, бронзы, мельхиора) и тугоплавких металлов.
Защита флюсами и газом
Сваривание металла под слоем флюса обычно выполняется автоматически или при наполовину автоматизированном процессе (полуавтоматом). В первом случае все процессы автоматизированы, во втором процесс подачи электрода производится автоматически, а движение горелки осуществляется сварщиком.
Расплав в сварочной ванне защищается расплавом шлака от воздействия атмосферного воздуха. Шлак получается за счет расплавления флюса поступающего в ванну. Вид сварки с применением флюсов весьма производителен, к тому же получается качественный сварной шов без пор и других недостатков.
Сваривание в газе обеспечивает предохранение участка сварки от вредного воздействия паров воды, атмосферного кислорода и азота.
Это обеспечивается за счет подачи струи защитного газа через сопло горелки в сварочную зону, что позволяет вытеснить атмосферный воздух. Используется при применении неплавящихся и плавящихся электродов. В итоге получается качественный шов при высокой производительности труда.
Электрошлаковая
Электрошлаковый вид сварки осуществляется благодаря сплавлению вертикальных краев изделия с электродом. Когда электрический ток проходит через лак, выделяется тепло. Дуга присутствует только на начальном этапе. В дальнейшем металл расплавляется за счет тепла выделяемого шлаком.
С двух сторон зазора устанавливаются ползуны из меди. Их охлаждают путем подачи воды. Снизу устанавливается поддон с флюсом. Между ним и электродом разжигают дугу и подают туда проволоку.
Электрическая дуга расплавляет проволоку и флюс, из них образуется сварочная ванна, над которой всплывает легкий жидкий шлак. По мере расплавления кромок и сварочной проволоки ползуны перемещаются вверх по стыку. В итоге получается качественный шов. Благодаря такому процессу можно варить металлы большой толщины за один проход.
Лучевая
В промышленности, особенно приборостроении и электронике требуется сваривать очень мелкие детали, имеющие особые требования к процессу сварки. Выбор способа сварки в этом случае невелик. С ними могут справиться только мощный световой луч, поток электронов или плазмы.
Чтобы получить шов отличного качества, требуется высокоэнергетический источник. Это может быть лазер или другой подобный источник энергии способный сконцентрировать огромную тепловую энергию на маленьком участке и на малое время. использует энергию разогнанных до большой скорости электронов. В случае с лазером разогрев осуществляется за счет энергии фотонов.
Плазма, газ, термическая реакция
Сущность вида сварки с применением плазмы заключается в формировании струи ионизированного газа, которая является проводником тока.
Температура плазмы достигает 30000 °C, что позволяет плавить любые металлы в кратчайшие сроки. Энергия плазмы зависит от величины сварочного тока, рабочего напряжения, расхода газа. Сварочные швы получаются высокого качества, тонкие, без внутренних напряжений.
Газовое сваривание осуществляется за счет сжигания горючего газа в кислороде и выделения большого количества теплоты. Это один из старейших видов сварки.
Температура газового пламени составляет три тысячи градусов. Благодаря этому расплавляются стыки свариваемого изделия. Процесс расплавления происходит долго, что вызывает нагрев больших участков поверхности соединяемых изделий. При охлаждении вызывает большие напряжения в шве и самой детали.
При термитном сваривании используется тепло выделяемое при сжигании смеси из алюминия и оксидов железа.
Термомеханическое сваривание материалов
К термомеханическому свариванию относится кузнечная, контактная и подобные им виды. Эти способы сваривания металла используют одномоментно тепловую и механическую энергию. К этому виду относят такие технологии:
- кузнечная;
- контактная;
- диффузионная;
Кузнечной сваркой называется способ, в котором свариваемые изделия сначала нагреваются до необходимой температуры в горне, а потом молотом соединяют друг с другом. Если вместо молота используется пресс, то такой способ называется прессовый.
Контактный вид имеет такое название благодаря тому, что сваривание осуществляется в месте контакта соединяемых деталей. Их сильно прижимают друг к другу с помощью специальных электродов, а затем через точку сдавливания пропускают мощный ток.
В месте контакта получается наибольшее сопротивление, что вызывает выделение основного тепла именно в этой точке. Соответственно, это приводит к расплавлению металла в точке контакта. С помощью контактной получают точечную или шовную сварку.
Контактная сварка получила широкое распространение в машиностроении, особенно в автомобилестроении. Это связано с высокой производительностью и экономичностью данного вида сварки. Она проще всего автоматизируется и широко используется в роботизированных комплексах.
Нельзя не упомянуть диффузионный вид сварки. Его сущность в предварительном нагреве заготовок и последующем их соединении с помощью деформации, которая возникает от механического давления. В таком процессе происходит диффузия атомов из одной соединяемой части в другую и получается неразрывное соединение.
Механическое сваривание материалов
При механическом способе сварки неразрывное соединение получают без внешнего источника тепла. Процесс соединения происходит под действием давления, трения, взрыва или чего-нибудь подобного, что образует межатомные связи между свариваемыми изделиями.
Сварка трением происходит в результате быстрого вращений. Она деталь так плотно прижата к другой, что при вращении происходит сильное трение и разогрев до расплавления. Это обеспечивает надежное соединение заготовок.
Если взять две металлические пластины, очистить от загрязнений и сильно прижать, то при давлениях в несколько десятков тысяч атмосфер происходит пластическая деформация, приводящая к образованию межатомных связей двух частей. В итоге получается неразрывное соединение. Такой способ называется холодной сваркой.
Чтобы возникли силы атомного взаимодействия, между двумя деталями иногда используется взрыв. В этот момент свариваемые детали сближаются так, что возникают атомные связи, которые обеспечивают надежное соединение изделий.
Еще один вид сварки – ультразвуковой. Высокочастотные волны вызывают колебания атомов в металле, и те становятся такими значительными, что вызывает атомные взаимодействия. Итог – надежное соединение.
Сварка http://weldex.kiev.ua/ – это один из самых долговечных и надежных способов крепления. Этот способ получил широкое применение в быту и промышленности из-за своей прочности, быстроты и экономичности. Ведущий вид сварки – электрический. С помощью электрического тока и электрода создается неразъемное соединение деталей. Сварочное оборудование http://weldex.kiev.ua/ballony/uglekislotnye-ballony/ уже целый век служит человечеству.
С помощью современных технологий стало возможным соединение сталей различного уровня легирования, а также некоторые цветные сплавы. На качество и стоимость работ влияют методы и тип решаемых задач.
В настоящее время используется достаточно много видов сварки. Рассмотрим самые распространенные.
Электродуговая сварка
При электродуговой сварке между электродом и заготовкой горит электрическая дуга, которая служит источником теплоты. Есть разные виды дуговой сварки. Они отличаются материалом и числом электродов, а также способом включения заготовки и электродов в цепь электрического тока. Бывает электродуговая сварка плавящимся электродом и неплавящимся электродом, трехфазной дугой и косвенной дугой.
Питание дуги осуществляется переменным и постоянным током.
Ручная дуговая сварка
При такой сварке сварочные электроды подают вручную в дугу и двигают вдоль заготовки. Электроды при таком виде сварки представляют собой стержни с покрытием. Сам стержень − это сварочная проволока высокого качества. В зависимости от состава сварочную проволоку подразделяют на группы: легированная, высоколегированная и низкоуглеродистая. Ток при ручной сварке ограничен из-за того, что его повышение сверх оптимального значения может привести к перегреву стержня, угару и разбрызгиванию металла, отслаиванию покрытия.
Автоматическая дуговая сварка под флюсом
При дуговой сварке под флюсом используют флюс для защиты сварочной ванны и дуги от воздуха, а также применяют непокрытую электродную проволоку. Механизированными являются процессы по перемещению и подаче электродной проволоки, а автоматизированными – зажигание дуги и заварка кратера в конце шва. Выполняют дуговую сварку под флюсом сварочными автоматами, самоходными тракторами, которые перемещаются по изделию, или сварочными головками. Применяется это вид сварки при изготовлении резервуаров, котлов, мостовых балок, корпусных сосудов и других изделий.
Электрошлаковая сварка и приплав
При этом виде сварки электродный и основной металлы расплавляются теплотой, которая выделяется при прохождении электричества через шлаковую ванну. Свариваемые заготовки при выполнении электрошлаковой сварки располагают вертикально. Шлаковая ванна в отличие от электрической дуги является более распределенным источником теплоты. Преимущества электрошлаковой ванны: лучшая макроструктура шва, повышенная производительность, меньшие затраты на выполнение одного метра шва.
Глава 1
Немного истории
1.1. Изобретение электросварки
1.2. Развитие электросварки в 20 веке
Глава 2
Основы дуговой сварки
2.1. Электрическая дуга
Физическая сущность
Вольтамперная характеристика
Ручная сварка на постоянном токе
Полуавтоматическая сварка на постоянном токе
Сварка на переменном токе
2.2. Процесс сварки
Сварка неплавящимся электродом
Сварка плавящимся электродом
Перенос металла
2.3. Основные характеристики источников питания сварочной дуги
Глава 3
Симулятор LTspice IV
3.1. Моделирование работы источника питания
Возможности моделирования
Программы моделирования электронных схем
Возможности программы LTspice IV
3.2. Работа программы LTspice IV
Запуск программы
Рисуем на ПК схему простейшего мультивибратора
Определение числовых параметров и типов компонентов схемы
Моделирование работы мультивибратора
3.3. Моделирование простейшего источника питания
Низковольтный источник постоянного тока
Тестовый узел
Глава 4
Сварочные источники переменного тока
4.1. Особенности терминологии
4.2. Основные требования к сварочному источнику
4.3. Модель электрической дуги переменного тока
4.4. Сварочный источник с балластным реостатом (активным сопротивлением)
4.5. Сварочный источник с линейным дросселем (индуктивным сопротивлением)
4.6. Сварочный трансформатор
4.7. Как рассчитать индуктивность рассеяния?
Индуктивность рассеяния трансформатора с цилиндрическими обмотками
Индуктивность рассеяния трансформатора с разнесенными обмотками
Индуктивность рассеяния трансформатора с дисковыми обмотками
4.8. Требования к сварочному трансформатору
4.9. Классический источник переменного тока
Расчет сварочного трансформатора с развитым магнитным рассеянием
Конструкция сварочного источника переменного тока
4.10. Сварочный источник Буденного
Пути уменьшения величины потребляемого тока
Конструктивно-электрическая схема сварочного источника Буденного
Общие принципы проектирования сварочного источника
Модель сварочного источника Буденного
Преодоление конструктивных ограничений сварочного источника Буденного
Определение габаритной мощности трансформатора
Выбор сердечника
Расчет обмоток
Расчет магнитного шунта
Расчет индуктивности рассеяния
Моделирование результатов расчета
Конструкция сварочного источника с альтернативной конструкцией трансформатора
4.11. Сварочный источник с резонансным конденсатором
Расчет сварочного источника с резонансным конденсатором
Расчет сварочного трансформатора
Проверка размещения обмоток в окне сварочного трансформатора
Расчет индуктивности рассеяния
Моделирование сварочного источника
4.12. Стабилизаторы дуги переменного тока
Особенности сварочной дуги переменного тока
Принцип действия стабилизатора дуги
Первая версия стабилизатора дуги
Детали
Вторая версия стабилизатора дуги
Детали
Глава 5
Сварочный источник для полуавтоматической сварки
5.1. Основы полуавтоматической сварки
5.2. Расчеты элементов схемы
Определение параметров и расчет силового трансформатора источника
Процедура настройки модели
Расчет омического сопротивления обмоток
Расчет индуктивности и сопротивления обмоток трансформатора
Расчет габаритных размеров трансформатора
Завершение расчета трансформатора
Расчет дросселя источника подпиточного тока
5.3. Описание конструкции простого источника для полуавтоматической сварки
Схема простого источника для полуавтоматической сварки
Детали для сварочного полуавтомата
Конструкция и изготовление сварочного трансформатора
Конструкция дросселя
Подключение источника
Глава 6
Сварочный источник для полуавтоматической сварки с тиристорным регулятором
6.1. Регулировка сварочного тока
6.2. Обеспечение непрерывности сварочного тока
6.3. Расчет сварочного трансформатора
6.4. Блок управления
6.5. Описание конструкции сварочного источника с тиристорным регулятором
Принципиальная электрическая схема
Детали
Конструкция сварочного трансформатора
Конструкция дросселя
Подключение источника
Глава 7
Электронный регулятор сварочного тока
7.1. Многопостовая сварка
Многопостовая сварка с подключением
через индивидуальный балластный реостат
Электронный аналог балластного реостата ЭРСТ
7.2. Расчет основных узлов ЭРСТ
7.3. Описание ЭРСТ
Основные варианты защиты
Назначение основных узлов ЭРСТ
Принцип действия
Принцип работы и настройка блока А1
Детали
Принцип работы и настройка блока А2
Принцип действия стабилизатора
Детали
Настройка
Формирование внешних характеристик ЭРСТ
Принцип работы блока управления ЭРСТ
Принцип работы блока драйвера ключевого транзистора
Завершающая настройка ЭРСТ
Глава 8
Инверторный сварочный источник
8.1. Немного истории
8.2. Общее описание источника
8.3. Рекомендации для самостоятельного изготовления ИСИ
8.4. Расчет трансформатора прямоходового преобразователя
8.5. Изготовление трансформатора
8.6. Расчет мощности потерь на транзисторах преобразователя
8.7. Расчет дросселя фильтра сварочного тока
8.8. Моделирование работы преобразователя
8.9. Расчет трансформатора тока
8.10. Расчет трансформатора гальванической развязки
8.11. ШИМ-контроллер TDA4718A
8.12. Принципиальная схема блока управления инверторного сварочного источника «RytmArc»
8.13. Формирование нагрузочной характеристики источника
8.14. Методика настройки БУ
8.15. Выносной пульт управления (модулятор)
8.16. Использование альтернативного ШИМ-контроллера
8.17. Трансформаторный драйвер
8.18. Демпфирующая цепь, не рассеивающая энергию
Глава 9
Инверторный сварочный источник COLT-1300
9.1. Общее описание
О чем эта глава
Назначение
Основные характеристики
9.2. Силовая часть
Данные моточных узлов
9.3. Блок управления
Функциональная схема
Принцип действия
Принципиальная схема
Реализация функции Anty-Stick
Реализация функции Arc Force
9.4. Настройка
Глава 10
Полезная информация
10.1. Как испытать неизвестное железо?
10.2. Как рассчитать трансформатор?
10.3. Как рассчитать дроссель с сердечником?
Особенности расчета
Пример расчета дросселя № 1
Пример расчета дросселя № 2
Пример расчета дросселя № 3
10.4. Расчет дросселей с порошковым сердечником
Преимущества порошковых сердечников
Адрес программы Inductor Design Software и ее установка
Функции автоматического расчета программы Inductor Design Software
Дополнительные функции программы Inductor Design Software
Панель меню программы Inductor Design Software
Пример расчета дросселя в программе Inductor Design Software
Программа Magnetics Inductor Design Using Powder Cores
Пример расчета дросселя в программе Magnetics Inductor Design Using Powder Cores
10.5. Как рассчитать радиатор?
10.6. Гистерезисная модель нелинейной индуктивности симулятора LTspice
Краткое описание гистерезисной модели нелинейной индуктивности
Подбор параметров гистерезисной модели нелинейной индуктивности
10.7. Моделирование сложных электромагнитных компонентов при помощи LTspice
Проблема моделирования
Принцип подобия электрических и магнитных цепей
Двойственность физических цепей
Модель неразветвленной магнитной цепи
Моделирование разветвленной магнитной цепи
Моделирование сложной магнитной цепи
Адаптация модели для магнитных цепей, работающих с частичным или полным подмагничиванием
Создание модели интегрированного магнитного компонента
10.8. Как изготовить сварочные электроды?